Marine Engineering
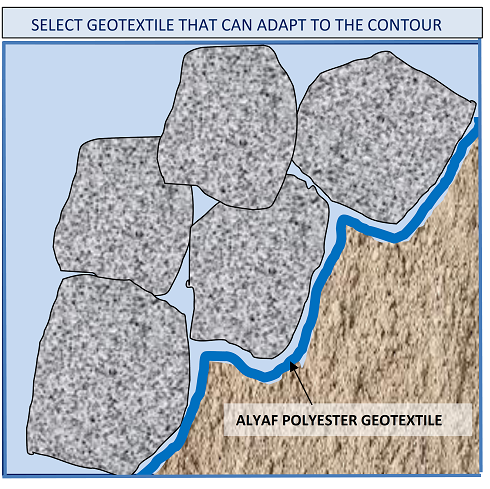
NEED FOR GEOTEXTILES
Flowing water can cause severe erosion and instability of soil structures. They are susceptible to erosion by water even at very low flow rates. The tradational protection works in river bank or shore protection structures envisage constructing flexible structures such as rip-rap or heavy armour stones to break up the water forces. When such highly permeable revetments are used to dissipate the hydraulic forces, turbulence occurs within the interstices of the revetment structure resulting in erosion of the base soil through the pores in the facing. To prevent washing away of the underlying soil, layers of granular materials, known as graded filters are placed between underlying soil and the highly permeable rip-rap. A typical graded filter may consist of successive layers of aggregates, the sizes of which are specifically designed.
The graded filter layers should be such that their particles should be fine enough so as to prevent erosion of the filter material beneath and large enough to prevent erosion of the filter material itself through the more permeable granular layer. If the hydraulic forces acting on a permeable erosion control structure are large, then the conventional design procedure would show a requirement of more than one granular layer to protect the base soil from erosion. Further, since it is desirable to reduce the head loss due to percolation through the filter to the smallest value compatible with the grain size requirement, large filters are usually made up of several layers. Since the first ever use of filter fabric as an alternative to a granular filter in 1958 in the reconstruction of a waterfront concrete block revetment in storm-lashed coast of Florida, USA, geotextiles have been extensively used in erosion control structures.
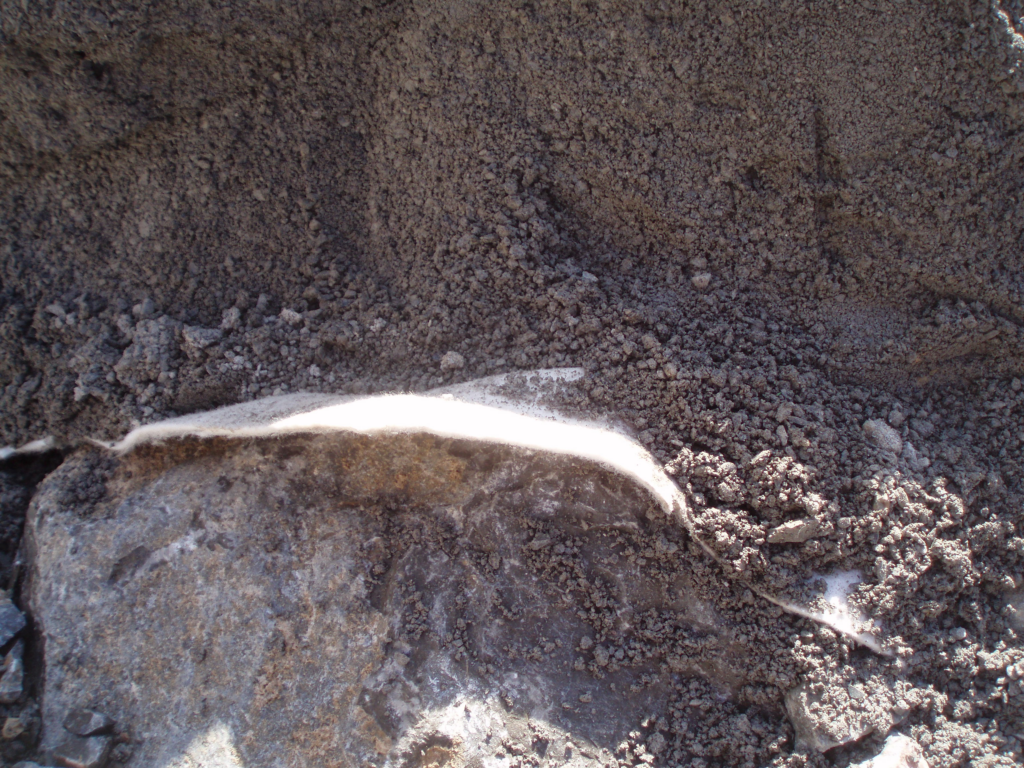
The graded filter layers should be such that their particles should be fine enough so as to prevent erosion of the filter material beneath and large enough to prevent erosion of the filter material itself through the more permeable granular layer. If the hydraulic forces acting on a permeable erosion control structure are large, then the conventional design procedure would show a requirement of more than one granular layer to protect the base soil from erosion. Further, since it is desirable to reduce the head loss due to percolation through the filter to the smallest value compatible with the grain size requirement, large filters are usually made up of several layers. Since the first ever use of filter fabric as an alternative to a granular filter in 1958 in the reconstruction of a waterfront concrete block revetment in storm-lashed coast of Florida, USA, geotextiles have been extensively used in erosion control structures.
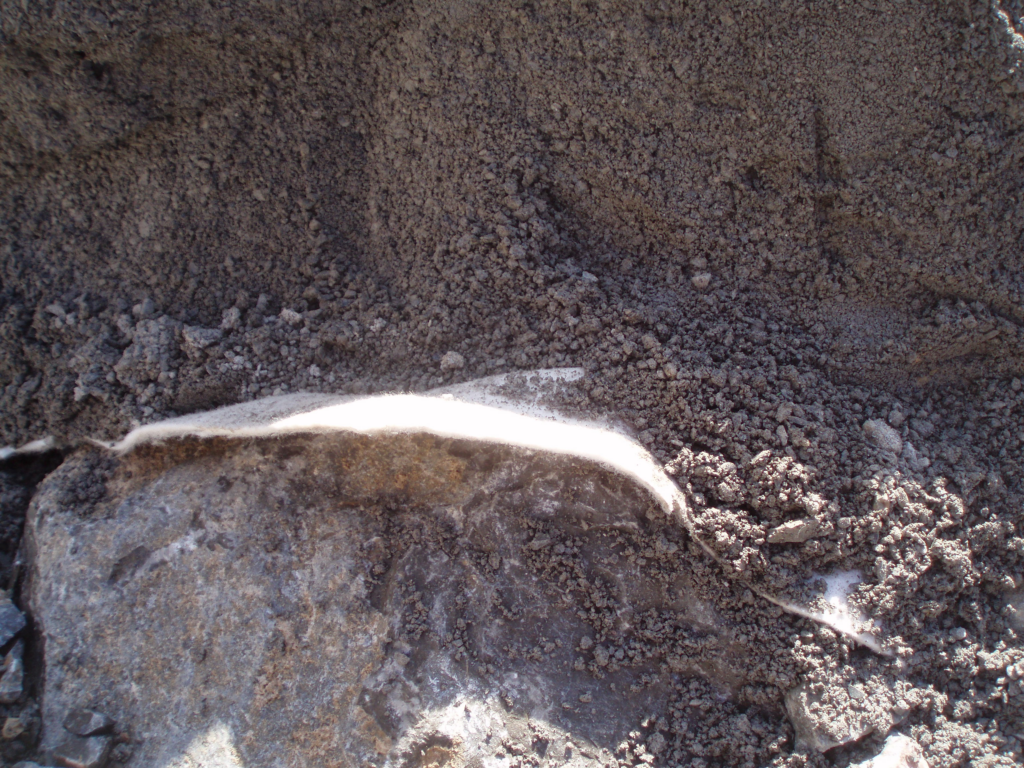
ADVANTAGES
For Erosion Control, Alyaf geotextiles are used as replacement for graded filters because they offer.
- Improved performance
- Considerable economy
- Consistent properties
- Ease of placement
APPLICATIONS
- Quay walls
- Seashore erosion protection
- Stream banks protection
- Ditch, channel and canal slope protection
- Cut and fill slope
- Scour protection around bridge piers.
- Rip-rap or heavy armour stone
- Concrete blocks
- Articulated concrete mattresses
- Gabion mattresses
Primary Functions
The primary functions of ALYAF geotextiles in erosion control applications are separation and filtration.
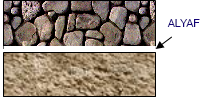
Separation
Separation is defined as, “The introduction of a flexible porous textile placed between dissimilar materials so that the integrity and the functioning of both the materials can remain intact or be improved” (Koerner, 1993).
Filtration
Filtration is defined as “the equilibrium geotextile-to-soil system that allows for adequate liquid flow with limited soil loss across the plane of the geotextile over a service lifetime compatible with the application under consideration“ (Koerner, 1993). To perform this function the geotextile needs to satisfy two conflicting requirements: the filter’s pore size must be small enough to retain fine soil particles while the geotextile should permit relatively unimpeded flow of water.
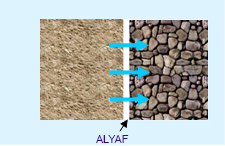
GEOTEXTILE REQUIREMENTS
The geotextile filter design criteria provided herein covers most areas of application where the geotextile is expected to act as a filter, either as a replacement for, or in conjunction with conventional graded filters.
ALYAF geotextiles
Designing with ALYAF geotextiles for filtration is essentially the same as designing with graded filters. Based on the analogy to soil filter design criteria, the following design criteria for Alyaf geotextiles is stated
- The geotextile must retain the soil fines (retention criterion), while
- Allowing a relatively unimpeded flow of water (permeability criterion), throughout the life of the structure (clogging resistance criterion).
- To perform effectively, the geotextile must survive the installationprocess (survivability criterion).
The design procedure proposed is based on the above stated parameters and the design procedure developed by Christopher and Holtz (Geosynthetic Engineering, 1985).
Retention Criteria
Dynamic flow or cyclic flow conditions exists particularly in erosion control systems. In this case, the bridging network will not be created and the geotextile is expected to retain the finest soil particles, hence the factor B should be reduced to 0.5 or AOS or O95 (geotextile) < 0.5 D85 (soil)
Clogging Resistance
Geotextile porosity, n > 70%.
For severe / critical conditions where soils potential to clog are addressed it is recommended that soil-geotextile clogging tests like the gradient ratio test [ASTM D 5102] are conducted. Alyaf nonwoven geotextiles being mechanically bonded through needle punching provide a very large number of small pores. This high level of porosity in the fabric structure reduces the probability of the geotextile from getting clogged. That is, even if a few pores get clogged over time it will not significantly reduce the overall system permeability.
Permeability Criteria
For less critical applications:
kgeotextile ≥ ksoil
For critical applications:
kgeotextile ≥ 10 ksoil
Where:
ksoil is the Darcy’s coefficient of permeability (m / sec.) of the soil to be filtered.
kgeotextile is the permeability coefficient of the geotextile
Survivability Criteria
This refers to the geotextile’s ability to withstand the installation stresses and perform as intended in the project design. Table on the cover back page gives the minimum physical property requirements for erosion control applications. These minimum survivability requirements are based on the experience on the properties of geotextiles, which have known to have performed satisfactorily in these applications.
POLYMER OF CHOICE
While geotextiles made from polyesters or polyolefin’s are recommended by independent agencies, due to their non-biodegradability and resistance to chemicals in seawater environment. In applications involving under water placement of geotextiles, polyester fiber based geotextiles should be the preferred choice because polyester has a specific gravity of 1.38 whereas polyolefin’s have specific gravity of 0.91. Seawater typically exhibits a specific gravity of 1.2; in this scenario when geotextiles with lower specific gravity are installed underwater, the buoyancy effect will make the installation extremely difficult. Further, these buoyancy forces continue to act during the life of the project causing soil migration from underneath the geotextile where it is not completely weighed down by the rock armour. This may lead to destabilization of the revetment.
Geotextile Specifications For Erosion Control
Test method | Unit | High Survivability | Moderate Survivability | |||||
---|---|---|---|---|---|---|---|---|
Property | ||||||||
AX11 | A901 | A701 | A601 | A501 | A401 | |||
CBR Puncture resistance | EN ISO 12236 | N | 10000 | 9000 | 6400 | 5400 | 4200 | 3200 |
Dynamic puncture (hole diameter) | EN 918 | mm | 0 | 2 | 4 | 5 | 8 | 12 |
Burst strength | ASTM D 3786 | kPa | 8960 | 7580 | 5950 | 4860 | 4800 | 3070 |
Tensile strength (CD/ MD) | EN ISO 10319 | kN | 72/40 | 62/34 | 52/26 | 42/22 | 30/16 | 24/14 |
Elongation at break | EN ISO 10319 | % | 50 | 50 | 50 | 50 | 50 | 50 |
Permeability | EN ISO 11058 | 10-3ms-1 | 16 | 22 | 30 | 40 | 53 | 60 |
Permeability coefficient | ASTM D4491 | cm/sec | 0.25 | 0.25 | 0.25 | 0.25 | 0.25 | 0.25 |
Pore Size (O90) | EN ISO 12956 | microns | 65 | 65 | 67 | 67 | 70 | 75 |
Notes:
High-survivability erosion applications for geotextiles are where set up stresses are more extreme than mild applications, i.e., where stone weights immediately in contact with geotextile exceed 100 kgs. and/or drop weight exceed one meter.
Moderate-survivability erosion applications are those where stone weights directly in contact with geotextiles does not exceed 100 kgs and drop height is less than one meter.
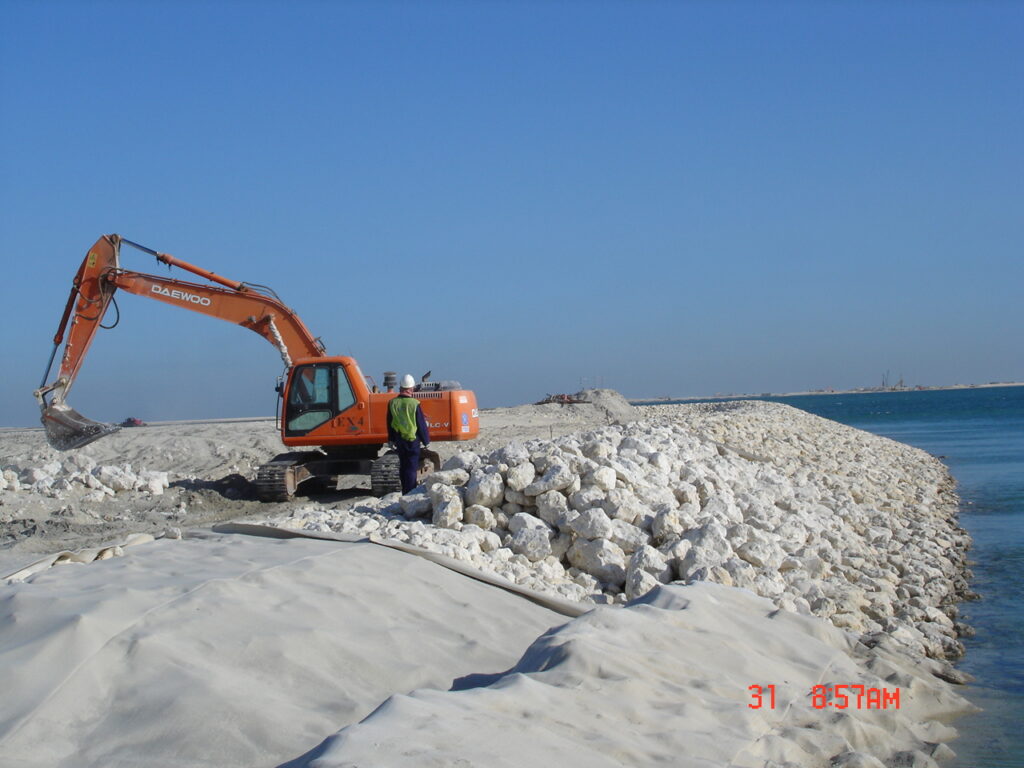
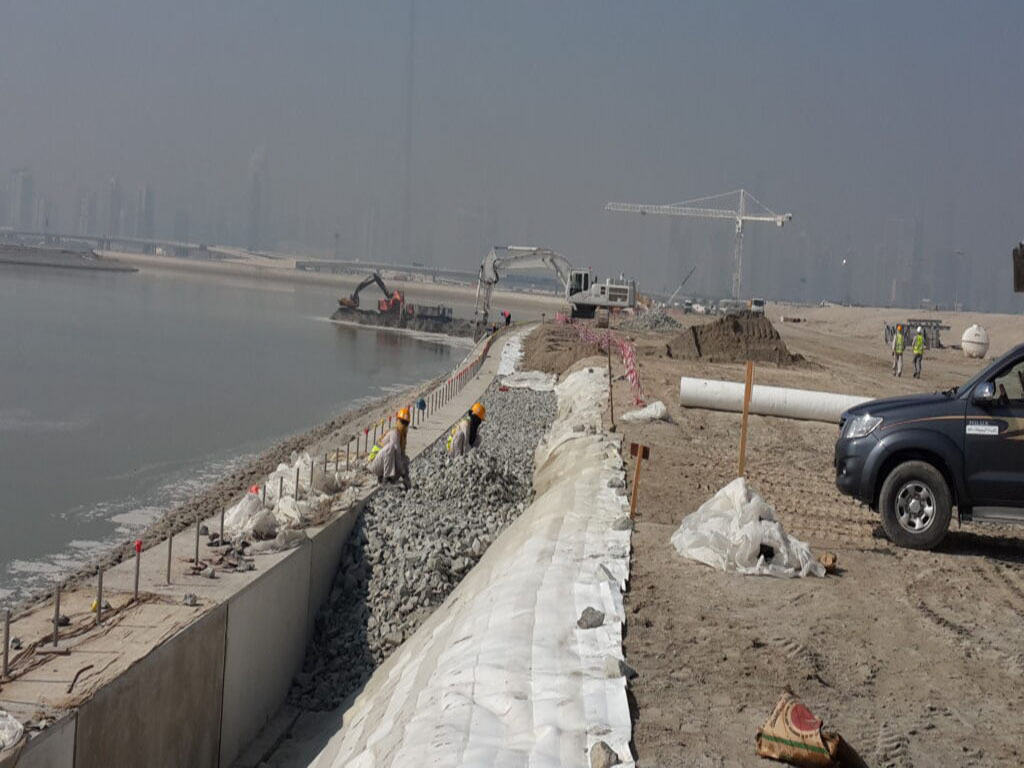
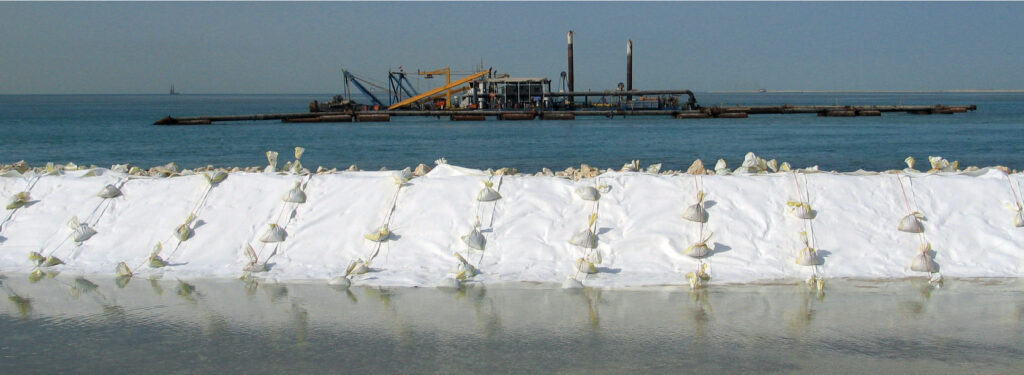